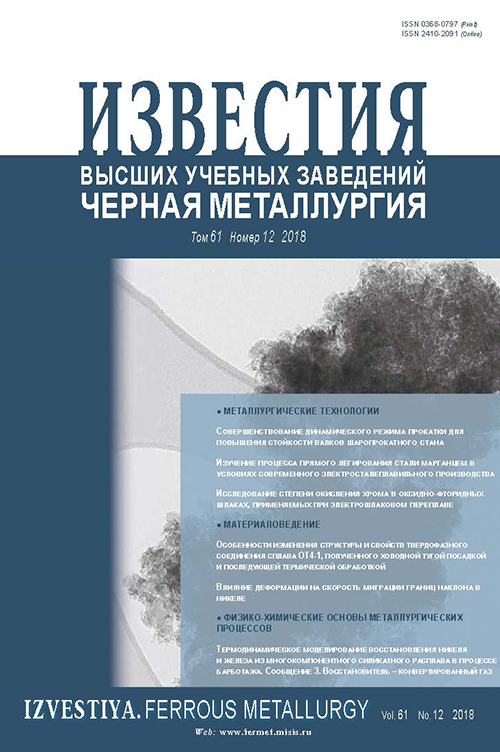
Научно-технический и научно-производственный журнал "Известия высших учебных заведений. Черная Металлургия"
DOI: https://doi.org/10.17073/0368-0797
Издается с января 1958 года.
Журнал публикует результаты фундаментальных, прикладных и научных исследований по актуальным вопросам черной металлургии.
Основные разделы журнала: Металлургические технологии; Ресурсосбережение в черной металлургии; Экология и рациональное природопользование; Инновации в металлургическом промышленном и лабораторном оборудовании, технологиях и материалах; Наука - производству; Информационные технологии и автоматизация в черной металлургии; Физико-химические основы металлургических процессов;Материаловедение; Стали особого назначения; Экономическая эффективность металлургического производства.
Журнал входит в «Перечень ведущих рецензируемых научных журналов и изданий, в которых должны быть опубликованы основные научные результаты диссертаций на соискание ученых степеней доктора и кандидата наук». Приравнивание научных журналов, входящих в наукометрические базы данных, к журналам Перечня ВАК с распределением по категориям.
Журнал включен в Scopus (с 2017 г.), Russian Science Citation Index на платформе Web of Science, Research Bible, OCLC и Google Scholar.
Журнал "Известия высших учебных заведений. Черная металлургия" принимает к рассмотрению статьи как на русском, так и на английском языке от российских и иностранных авторов. Англоязычная статья может быть представлена в международной базе данных SCOPUS в полном варианте. Редакция готова предоставить услуги по переводу русского текста на английский в случае заинтересованности автора.
Учредители - Национальный исследовательский технологический университет «МИСИС» и Сибирский государственный индустриальный институт. Издатель - Национальный исследовательский технологический университет «МИСИС». С 2023 года журнал выходит 6 раз в год.
Текущий выпуск
МЕТАЛЛУРГИЧЕСКИЕ ТЕХНОЛОГИИ
Физическим моделированием с использованием вертикальной трубчатой электропечи оценили распределение масла из замасленной окалины между различными видами отходов газоочистки доменного производства: пылью, шламом и шламовой водой. Согласно математическому моделированию теплового состояния металлического контейнера с замасленной окалиной интенсивное испарение масла в доменной печи начинается после его загрузки и опускания вдоль шахты на глубину, примерно соответствующую трем подачам. Масло пропускали через нагретый до 500 °C слой агломерата и окатышей Михайловского ГОК массой 0,6 кг и крупностью частиц 10 – 12 мм. Вместе с парами масла в слой железорудного сырья (ЖРС) подавали (вдували) тонко измельченный материал, имитировавший по компонентному и фракционному составам смесь колошниковой пыли и шламов вакуумной фильтровальной установки (ВФУ) доменного производства, взятых в соотношении 36:64. Физическое моделирование обеспечивало соответствие фактическому газодинамическому режиму в зоне рудного гребня доменной печи, исходя из равенства критерия Рейнольдса. Значение этого критерия, равное 215, было достигнуто в лабораторной модели при подаче аргона с расходом 70 л/мин. По результатам эксперимента распределение масла составило, % от исходного количества: 74,8 % разложилось на слое ЖРС, соответствующем трем подачам; 9,1 % перешло в колошниковую пыль; 15,9 % перешло в шлам ВФУ; в воде мокрой газоочистки масло отсутствовало; 0,2 % (30 мг) масла проходило мокрую газоочистку в форме аэрозоля; на стенках трубопровода наблюдалось незначительное количество сажи. Газовая фаза процессов разложения масла содержала: 70 – 90 % H2 ; 1 – 5 % CO; 0,5 – 7,0 % CO2 ; 3,2 – 22,2 % СH4 ; 0,1 – 2,5 % Σ(C2H4 , C2H6 , C3H6 , C3H8 ). Содержание контролируемого в России бензо(а)пирена в парах масла не превышало 0,00058 %.
На электролитической модели авторы исследовали работу ферросплавной печи при увеличении диаметра электродов и повышении мощности. В качестве рабочего тела использовали традиционный водный раствор c концентрацией 0,2 % NaCl. Диаметр электродов увеличивали от 30 до 150 мм. Параметры печей мощностью от 7,5 – 10,5 до 81 МВ·А при выплавке ферросилиция соответствуют результатам опытов моделирования, которые были подтверждены при выплавке 45 %-ного ферросилиция в промышленных печах с аналогичными относительными технологическими параметрами. Вид зависимости снижения сопротивления ванны от увеличения диаметра электродов для промышленных ферросплавных печей аналогичен зависимости, полученной в результате опытов по моделированию. Фактор значительного снижения сопротивления ванны от увеличения диаметра электрода для ферросплавных печей различной мощности при выплавке одного сплава имеет весьма существенное значение. При увеличении силы тока электрода снижаются электрический КПД, коэффициент мощности печи и доля активной мощности в ванне технологического процесса. Проведенный анализ параметров печей при выплавке 45 %-ного ферросилиция подтверждает выводы электролитического моделирования ферросплавных печей о значительной роли увеличения диаметра электродов печей в снижении активного сопротивления ванны.
ЭКОЛОГИЯ И РАЦИОНАЛЬНОЕ ПРИРОДОПОЛЬЗОВАНИЕ
Газовый анализ – один из ключевых методов оценки качества атмосферного воздуха в населенных пунктах, а также в рабочей зоне производств. Особенно необходим мониторинг атмосферного воздуха на объектах, оказывающих значительное негативное воздействие на окружающую среду, в частности, на предприятиях черной металлургии. Особенность газоанализаторов, используемых для системы наблюдения за качеством воздуха, заключается в их чувствительности и селективности. Для достижения данных показателей необходим правильно подобранный чувствительный элемент: преобразователь газоанализатора. В качестве материалов для изготовления преобразователей предлагаются синтезированные твердые растворы полупроводниковых бинарных компонентов, которые зарекомендовали себя как хорошие адсорбенты. В настоящей работе авторы рассмотрели полупроводниковые системы, состоящие из ZnTe и CdSe, условия синтеза твердых растворов на их основе, способы их идентификации, которые позволили аттестовать полученные материалы как твердые растворы замещения с кубической структурой (сфалерита) и гексагональной структурой (вюрцита) (в зависимости от состава). Выполненные рентгенографические, микро-, электронно-микроскопические, ИК-спектроскопические исследования твердых растворов позволили понять структуру поверхности адсорбентов. Результаты исследований химического состава поверхности, кислотно-основных свойств твердых растворов и бинарных компонентов систем позволяют сделать вывод о присутствии на поверхности льисовских и бренстедовских кислотных центров, отвечающих за адсорбцию СО на поверхности. В системах ZnTe – CdSe наблюдается тенденция перехода от слабокислой области к относительному повышению основности поверхности с увеличением содержания ZnTe. При помещении материалов в атмосферу СО в такой же зависимости происходит адсорбция газа на поверхности твердых растворов, что подтвердили прямые каталитические исследования. Установленные закономерности изменений с составом объемных и поверхностных свойств позволяют рекомендовать новые полученные материалы в качестве первичных преобразователей сенсоров-датчиков.
МАТЕРИАЛОВЕДЕНИЕ
Созданный в начале XXI века новый класс материалов – высокоэнтропийные сплавы – привлекает внимание исследователей в области физического материаловедения. На основе анализа литературных данных последних лет рассмотрено современное состояние проблемы создания и исследования средне- и высокоэнтропийных быстрорежущих сталей. Благодаря твердорастворному упрочнению и упрочнению нановыделениями на основе средне- и высокоэнтропийных сплавов сложного состава возможно создание быстрорежущих сталей с высокими твердостью, термической стойкостью и ударной вязкостью. Приведенные результаты исследований трибологических характеристик и микротвердости быстрорежущих сталей свидетельствуют о зависимости этих характеристик от энтропии. Наименьшие значения сил резания и контактных температур характерны для режущего инструмента из быстрорежущей стали с высоким уровнем энтропии. Таким образом, при разработке новых быстрорежущих марок предпочтение следует отдавать составам с высоким уровнем энтропии, поскольку они обеспечивают лучшие трибологические характеристики и более высокую износостойкость. Методами современного физического материаловедения изучено структурно-фазовое состояние наплавки в среде азота высокоэнтропийной быстрорежущей молибденовой стали неэквиатомного состава на среднеуглеродистую сталь. Методами рентгеноспектрального анализа определен элементный состав поверхностного слоя наплавки, а рентгенофазным анализом установлено, что твердые растворы на основе α-железа (88 мас. %) и γ-железа (12 мас. %) являются основными фазами материала наплавленного слоя. Проведенный расчет конфигурационной энтропии данной быстрорежущей высокоэнтропийной стали дает значение 1,93R (где R – универсальная газовая постоянная). Сделан вывод об актуальности и перспективах разработки и исследования высокоэнтропийных сплавов.
Рассматриваемый аналитический метод определения оптимального режима упрочняющей импульсной лазерной обработки (ЛО) вольфрамокобальтовых твердых сплавов основан на исследовании закономерностей формирования температурного поля при упрочнении твердых сплавов, определении термических напряжений, возникающих в зоне лазерного воздействия (ЗЛВ) при лазерной импульсной обработке, и сравнении их с напряжениями разрушения отдельных структурных элементов сплава. Оптимальными режимами упрочняющей ЛО сплавов группы ВК считаются режимы, удовлетворяющие двум критериям. Во-первых, температура на поверхности ЗЛВ должна находиться в интервале 1290 °С < T < 1400 °С, когда в ЗЛВ не присутствуют разупрочняющие сплав фазы типов η-Co3W3C, θ-Co3W2C, χ-Co3W9C4 , а укрупнение зерен карбидной фазы незначительно. Во-вторых, в ЗЛВ недопустимо появление трещин произвольного масштаба, то есть термические напряжения, возникающие в результате ЛО, не должны превышать напряжений разрушения структурных элементов сплава. Расчет термических напряжений, возникающих в твердом сплаве при лазерной обработке в пределах одного карбидного зерна, выполняется в соответствии с законом Гука. Расчеты, выполненные как для однократной, так и для многократной обработки, позволяют установить, что для всех исследованных режимов при вариации плотности энергии лазерного излучения от 0,9 до 1,8 Дж/мм2 и кратности обработки от 1 до 10, когда температура на поверхности находится в диапазоне 1290 ‒ 1400 °С, термические напряжения в карбидной фазе меньше минимальных напряжений разрушения и не превосходят 80 МПа. Предложенный аналитический метод определения предельных энергетических характеристик позволяет установить режимы импульсной ЛО, которые обеспечивают дисперсионное упрочнение твердых сплавов вольфрамокобальтовой группы при отсутствии деструктивных изменений в ЗЛВ. Полученные данные о режимах бездефектной лазерной обработки хорошо согласуются с более ранними результатами измерений сигнала акустической эмиссии при обработке твердых сплавов (сплава ВК8).
ИННОВАЦИИ В МЕТАЛЛУРГИЧЕСКОМ ПРОМЫШЛЕННОМ И ЛАБОРАТОРНОМ ОБОРУДОВАНИИ, ТЕХНОЛОГИЯХ И МАТЕРИАЛАХ
В статье решается задача определения температуры калиброванных бойков установки совмещенного литья и деформации при получении стальных полых заготовок. Авторы обосновывают актуальность определения температурных полей и термоупругих напряжений в калиброванных бойках при обжатии стенки полой заготовки и на холостом ходу при охлаждении бойков водой, приводят прочностные и теплофизические свойства стали, из которой изготовлены бойки. Показана геометрия бойка для получения полой заготовки за один проход. Приводятся исходные данные для расчета температурного поля бойка установки совмещенного литья и деформации при получении полых заготовок, а также представлены температурные граничные условия для расчета температурных полей бойков. Статья описывает граничные условия для определения температуры бойка и значения теплового потока и эффективного коэффициента теплоотдачи. Результаты расчета температурных полей были выполнены в четырех сечениях для характерных линий и точек, расположенных на контактной поверхности бойка и в приконтактном слое на глубине 5 мм от рабочей поверхности. Размеры сетки конечных элементов приведены для использования при расчете температурного поля бойков. Температурное поле бойков с буртами определялось на основе решения уравнения нестационарной теплопроводности с соответствующими начальными и граничными условиями. Представлены величины и закономерности распределения температуры в калиброванном бойке при обжатии стенки полой заготовки и на холостом ходу при получении за один проход полой заготовки на установке совмещенного литья и деформации.
Задачей настоящего теоретического исследования является оценка влияния кольцевых температурных швов на внутренней поверхности литейной металлической сферической формы на уровень напряженно-деформированного состояния (НДС) в ней при кристаллизации стальной отливки. Специфика данного технологического процесса состоит в геометрической форме (сфера) литейной модели, когда кристаллизующийся металл создает во внутренней поверхности литейной формы (в первые мгновения) значительные сжимающие напряжения, которые усиливаются кривизной формы: внутренний слой формы, нагреваясь, пытается увеличиться в объеме, но этому препятствуют не только более холодные внешние слои, но и кривизна самого поверхностного слоя. Рассматриваются два варианта применения литейной формы: со швами и без них. Формулируется задача оптимизации конструктивных параметров температурных швов (выточек) от величины возникающих в литейной форме нормальных напряжений в начальной стадии кристаллизации стальной отливки. При решении задачи используются уравнения линейной теории упругости, уравнения теплопроводности и апробированный численный метод. Приведена численная схема и разработанный алгоритм решения задачи. Оценка трещиностойкости проводится по величине нормальных напряжений в металлической сферической форме. Найденные в результате решения тестовой задачи оптимальные конструктивные варианты (схемы) литейной сферической металлической формы зависят от расположения температурных швов в оболочковой форме, значений напряжений в них в условиях целевой функции min-max и разработанного алгоритма. Результаты решения задачи представлены графически в виде эпюр напряжений и температур по исследуемой области в разных сечениях и временах охлаждения ОФ и нарастающей корочки металла. Дан анализ полученных результатов стойкости металлической сферической литейной формы.
Рассмотрены особенности процесса получения гранулированного чугуна с применением кольцевой печи с вращающимся подом при реализации технологии ITmk3 (Ironmaking Technology Mark Three). Авторы показывают конструкцию угольного газификатора с системой очистки синтезируемого газа и поперечное сечение кольцевой печи. Статья кратко описывает процесс промышленного получения гранулированного высококачественного чугуна. Проведена оценка перспективы использования рассматриваемой технологии на территории Российской Федерации. На первом этапе исследований металлизации железорудного концентрата (ЖРК) углем применен термогравиметрический метод полного факторного эксперимента по определению оптимальных условий металлизации. В экспериментах варьировали соотношение ЖРК: уголь, крупность угля, добавки извести в процентах от суммы (ЖРК + уголь). В результате термогравиметрического анализа авторы получили кривые изменения массы образцов, состава и количества выделившегося газа при изменении температуры нагрева в процессе спекания ЖРК с углем и известью. На втором этапе для отработки технологии ITmk3 разработана лабораторная камерная печь с выдвижным подом, отапливаемая генераторным газом из каменного угля. Рудно-угольные брикеты были изготовлены с соотношением ЖРК, уголь, бентонит 80:20:5 и термообработаны в камерной печи с отоплением генераторным газом из угольного газификатора. В качестве опытного сырья были использованы железорудный концентрат Коршуновского горно-обогатительного комбината и Касьяновский каменный уголь Черемховского месторождения. На основе лабораторных исследований был определен температурно-временной режим обжига рудно-угольных брикетов, обеспечивающий высокую степень металлизации железорудных материалов (80 – 87 %) при обжиге брикетов в диапазоне температур 1080 – 1424 °С в течение 40 мин. Выход брикетов после сушки и обжига составил 66,45 %. Авторы изучили механизмы твердофазного восстановления железорудных материалов в кольцевых печах с вращающимся подом и жидкофазного разделения продуктов восстановления, а также определили состав выделившихся газов при прокаливании рудно-угольных брикетов.
Статья посвящена актуальной теме повышения эффективности вращающихся печей, используемых при производстве металлургической извести из мела. Рассмотрены методы усовершенствования конструкций и тепловой работы этих агрегатов, что особенно важно в условиях современного производства. Работа начинается с описания значимости извести в металлургической отрасли и особенностей применения вращающихся печей как основных агрегатов для ее производства. Отмечена необходимость повышения производительности и снижения энергозатрат. В статье представлен обзор перспективных технических решений, таких как конструктивные изменения, оптимизация теплообменных устройств, совершенствование горелочных механизмов, внедрение систем автоматического контроля и управления технологическим процессом. Также рассмотрены результаты испытаний, подтверждающих целесообразность использования мела определенных марок. Авторы обращают внимание на важность таких факторов, как качество сырья и квалификация обслуживающего персонала, которые влияют на эффективность обжига. Предложены новые технические решения, позволяющие повышать эффективность процесса обжига и снижать энергозатраты. Изучены основные проблемы, связанные с производством извести из мела. Предлагаемые усовершенствования направлены на решение указанных в работе проблем и улучшение качества конечного продукта. Особое внимание уделено оптимизации теплового режима печи, что позволит более эффективно использовать тепловую энергию и снизить расход топлива, что в свою очередь приведет к снижению себестоимости производства извести. Реализация предложенных технических решений позволит значительно повысить экономическую и экологическую эффективность ее производства. Авторы подчеркивают, что продолжение исследований в данной области перспективно для улучшения эксплуатационных характеристик вращающихся печей и, соответственно, качества получаемого продукта.
ИНФОРМАЦИОННЫЕ ТЕХНОЛОГИИ И АВТОМАТИЗАЦИЯ В ЧЕРНОЙ МЕТАЛЛУРГИИ
В статье рассматривается разработка информационно-моделирующей системы оценки нестабильности функционирования доменной печи. Представленный подход базируется на применении математических моделей и методов анализа параметров доменного процесса, что позволяет оценивать влияние технологических и организационных факторов на стабильность работы печи. Разработанная система предназначена для автоматизированного сбора, обработки и анализа данных в реальном времени, а также прогнозирования технологических отклонений. В основе методики лежит использование интегральных показателей стабильности, включая технико-экономические характеристики плавки, свойства сырья, параметры дутьевого, газодинамического, теплового и шлакового режимов. Для расчета интегральных показателей применяется совокупность контролируемых и расчетных признаков, ранжированных по степени значимости. Основные модули системы включают функциональные блоки сбора данных, расчетов, анализа и визуализации. Архитектура системы реализована на основе клиент-серверного подхода, что обеспечивает возможность интеграции с существующими системами управления металлургическим производством. Практическая реализация системы позволяет улучшить показатели производительности доменной плавки, снизить колебания параметров технологического процесса и повысить качество получаемого чугуна. Приведенные примеры расчетов подтверждают эффективность разработанного инструмента. Представленные результаты могут быть полезны для специалистов в области автоматизации доменного производства, а также для исследователей, занимающихся анализом и прогнозированием нестабильности технологических процессов.
Главный горновой желоб доменной печи – это сложная технологическая конструкция, играющая критическую роль в процессе выплавки чугуна. Он служит для отвода расплавленного чугуна и шлака из горна печи, обеспечивая непрерывность и безопасность процесса. Надежная работа желоба напрямую влияет на производительность доменной печи. Конструкция желоба должна выдерживать экстремально высокие температуры и агрессивную химическую среду, а его правильное функционирование требует постоянного контроля и обслуживания. Корректный выбор огнеупорных материалов, технологии футерования, а также выявление возможности повышения стойкости огнеупорной футеровки главных горновых желобов и продления срока их службы определены своевременным получением информации о тепловой нагрузке на слои огнеупоров и кожух, об условиях эксплуатации, конструктивных особенностях и процессах разрушения огнеупоров при их взаимодействии с чугуном и шлаком. Системы контроля работы главного горнового желоба доменной печи призваны обеспечивать безопасную и эффективную его эксплуатацию, своевременно выявляя отклонения от нормального режима и предотвращая аварийные ситуации. Они включают в себя визуальный, инструментальный и автоматический контроль. Система мониторинга разгара главных горновых желобов позволит технологическому персоналу доменной печи контролировать состояние желобов, оценивать их остаточный ресурс и принимать своевременные решения об их ремонте. Разработанная математическая модель состояния футеровки главного желоба доменной печи учитывает термоконтроль кожухов горновых желобов в реальном времени. Она нацелена на получение оперативной информации по разгару главных горновых желобов и основана на решении задачи стационарной теплопроводности многослойной плоской стенки, каждый слой которой является однородной стенкой.
Известной причиной возникновения дефектов плоской формы на готовых стальных холоднокатаных полосах является неравенство коэффициентов вытяжки по ширине полосы. На разницу значений этих коэффициентов оказывают влияние параметры профилировок бочек валков, энергосиловые параметры прокатки, параметры работы системы автоматического регулирования профиля и формы полосы. Воздействие всех технологических факторов на форму полосы будет иметь сложный характер. В работе рассмотрен подход, учитывающий основные параметры работы прокатного оборудования и позволяющий оценить вид и амплитуду дефектов плоскостности готовых стальных полос. При реализации такого подхода выполнены шесть этапов расчета: энергосиловой расчет процесса холодной прокатки; расчет упругих деформаций поверхности бочки рабочего валка; оценка износа поверхности бочки рабочего валка; расчет теплового профиля валка; оценка выпуклости поперечного профиля стальной полосы; оценка показателей планшетности готовой полосы. Для вычисления параметров, влияющих на планшетность проката, использованы известные методики расчета, адаптированные под конкретные технологические условия. Результаты оценки показателей формы катаной полосы, полученные с помощью модели, сопоставлены с результатами моделирования в программе Deform 3D. Результаты моделирования продемонстрировали достоверность предложенного подхода оценки качества проката.
В ПОРЯДКЕ ДИСКУССИИ
Окисление и восстановление металлов заключаются в потере атомами металлов валентных электронов с преобразованием электромагнитной металлической связи в ионную при окислении и обратный переход электронов от анионов к катионам металла с превращением ионной связи в металлическую при восстановлении. Развиваемая авторами электронная теория восстановления описывает процесс восстановления последовательной работой двух электрохимических элементов: топливного, в котором химическая энергия окисляемого восстановителя превращается в электрическую энергию «свободных» электронов, и твердоэлектролитного электролизера, превращающего электрическую энергию этих электронов в энергию металлической связи восстанавливаемых катионов в оксиде. Так как стадией собственно восстановления является образование металлической связи между катионами за счет поступающих извне электронов, то самым коротким и потому самым эффективным будет подвод электронов к восстанавливаемым катионам не от топливного элемента, а из электрической сети, то есть электролиз оксидов восстанавливаемого металла. Известные способы получения железа электролизом расплавленных оксидов, а также, возможно, щелочных растворов являются перспективными при извлечении железа из богатых руд. Для селективного извлечения железа из железомарганцевых, титаномагнетитовых, сидеритовых, хромитовых и других комплексных руд более перспективным является относительно низкотемпературное восстановление железа водородом или твердофазный электролиз с получением после разделения продукта металлизации плавлением безуглеродистого железа и концентрата оксидов активных металлов.
ISSN 2410-2091 (Online)